Forging the missing link of Europe’s hydrogen value chain
Novel compressed H2 carrier design offers cost-competitive, energy-efficient regional energy transport, write ABS senior vice president, global engineering, Gareth Burton, and Provaris Energy chief technical officer, Per Roed
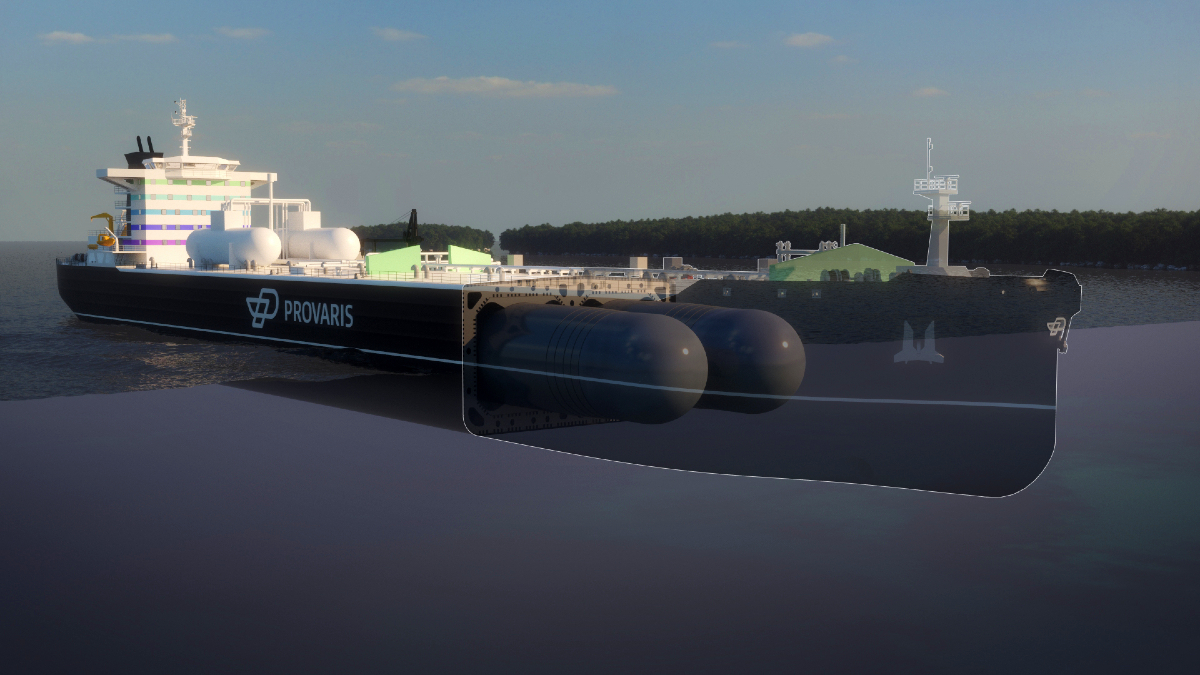
The energy transition is driving innovation across the maritime industry, as producers and consumers look to create opportunities from new value chains. The process comes with challenges, too; novel concepts call for first-time approaches that require detailed development work and a strong focus on safety.
Europe’s hydrogen value chain is developing at pace; the challenge is connecting producers with off-takers that will consume the clean energy delivered at the required cost and energy density.
When Australian clean hydrogen project developer Provaris unveiled the concept design for a compressed hydrogen carrier, it selected ABS as technical partner to provide class approvals for a ship that will close a gap in Europe’s clean energy supply chain.
Technology choices
For Provaris, the advanced stage of its H2Neo ship design underpins its operating model, providing an alternative to liquefaction for the transport of hydrogen or use of ammonia as a hydrogen carrier. While designs for liquefied hydrogen (LH2) and ammonia carriers have grabbed more of the headlines, the company has continued to develop shipping concepts based on compression technology, targeting an operational start by 2028.
This has involved striking collaboration agreements between producers in the Nordic countries and attracting the interest of leading German energy utilities, including Uniper. Germany in particular is a core market for hydrogen. The country currently imports 90% of its energy needs and demand for clean fuels could see imported hydrogen grow to reach between 1.5 to 3.0 tonnes annually by 2030.
To create the new value chain, final class approval of the innovative vessel design is the next milestone. The choice of compression technology is grounded firstly in economics.
In contrast to the shipping of ammonia (NH3) from which hydrogen can be extracted, transporting compressed hydrogen results in reduced loss of energy content of the delivered product by maintaining the hydrogen in a gaseous state. Though the economics shift in favour of ammonia carriers over longer voyages, on a regional voyage basis, compression requires lower capital outlay and delivers more energy to lower the overall cost of delivered hydrogen.
FEED level design approval
ABS awarded initial approval in principle (AiP) in 2021 for two classes of green compressed hydrogen (GH2) carriers, the 26,000-m3 H2Neo and 120,000-m3 H2Max. Provaris has taken the H2Neo through to construction-ready status and expects to issue an open tender to shipyards in 2025 for a vessel with delivery in 2027-28.
The company spent 12 months completing an extensive front end engineering design (FEED) package for the H2Neo. Design approval was granted in 2022, verifying the ship’s ability to transport compressed hydrogen in bulk at 250-bar pressure.
ABS affiliate ABS Consulting carried out hazardous risk and safety (HAZID) workshops and specialist studies concerning gas dispersion, explosion and fire analysis to help assess and mitigate the risks associated with the storage and transport of hydrogen.
This was the first time that an extensive HAZID and FEED-level design for a novel hydrogen carrier had been concluded. Provaris has continued to work with ABS through the subsequent phases of detailed production design, cargo tank testing and construction, with final class approval expected in due course.
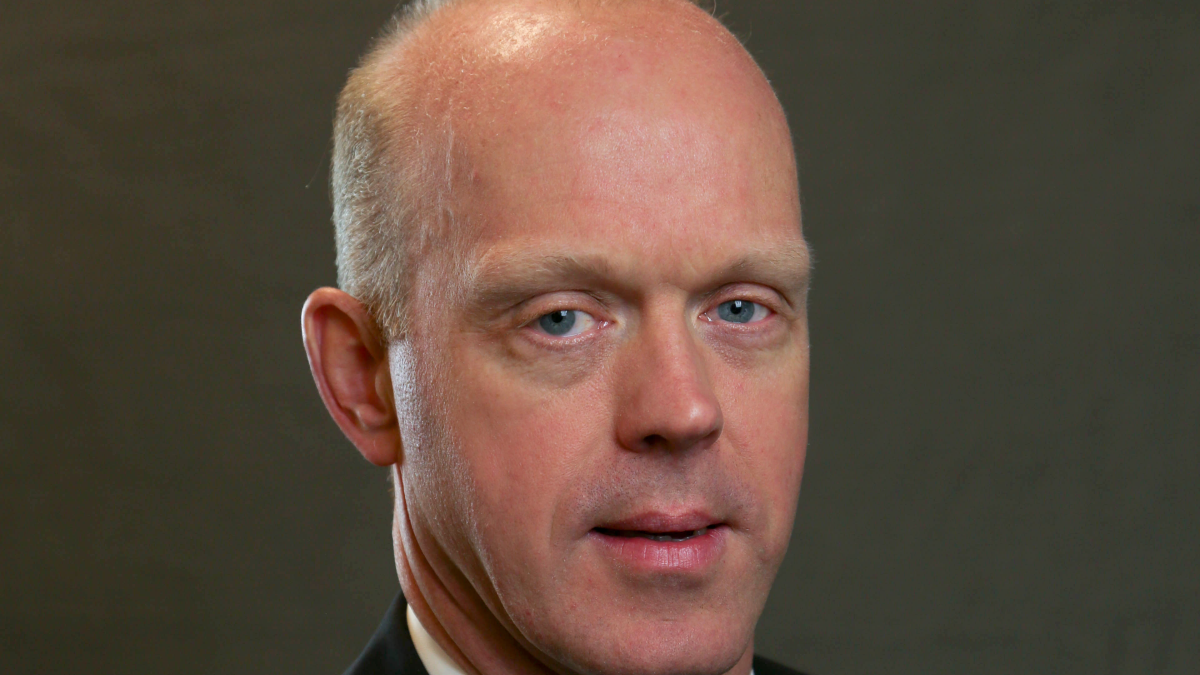
Design innovation
At the heart of the vessel design is a proprietary multi-layered hydrogen storage tank which required extensive design and structural assessment works for ship integration, as well as the creation of a digital twin for tank design and construction purposes. Optimisation through the development of a prototype tank will also focus on an automated robotic cell ready for a full-scale production line.
Key to a safe and sustainable process was a focus on safe handling for the hydrogen cargo with extensive risk analysis and mitigation built into the project backbone. To achieve this, the tanks are constructed in layers of carbon steel that are fully welded, with an internal liner that has been tested in a high-pressure hydrogen environment. A continuous monitoring system will be applied to verify the tank’s integrity. A single, fully welded header for loading and discharge is applied to limit the number of tank connections, and potential hydrogen leak points during cargo operations.
Provaris partnered with a Norwegian engineering firm to perform tank fabrication using robotic-laser welding to ensure precision and to eliminate a significant amount of associated labour cost. The robots are programmed for nanometer accuracy, verified through the prototype, delivering a very high quality of welding with proven fatigue life characteristics.
As with similar value chains for new fuels and cargo types, the approvals process depends on equivalency, as no specific regulations covering compressed hydrogen exist at present. The process required using elements of the IGF and IGC Codes as well as ABS’s own Guides for gas-carrying vessels.
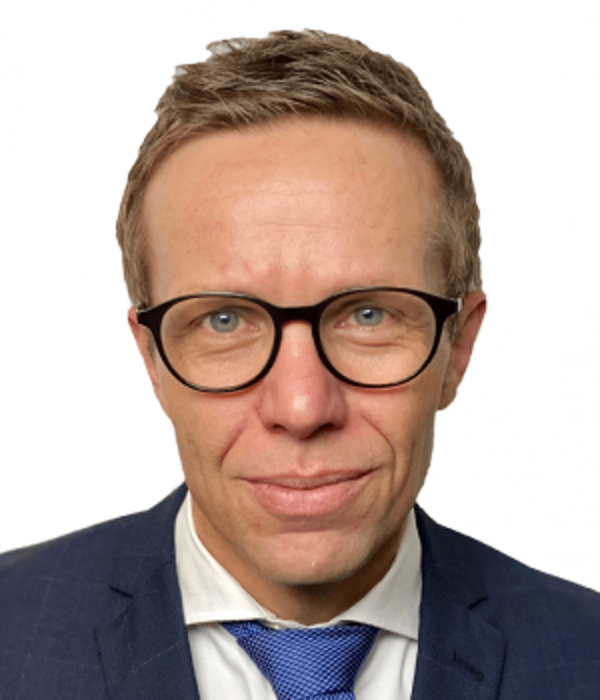
Extension to barge storage solutions with AIP
Leveraging the FEED-level engineering, safety studies and design approval for the H2Neo carrier received in December 2022, Provaris has launched the H2Leo compressed hydrogen floating storage solution, receiving AiP from ABS. The AiP allows for a flexible solution for specific industry applications with a design capacity range of 300 to 600 tonnes of hydrogen. The future development and approvals include expanding the storage capacity from 100 to 2,000 tonnes of hydrogen storage.
The H2Leo is a flexible hydrogen floating storage unit that can be optimised in size, capacity and operations for different applications. Its SIMOPs capability allows for continuous operations, and it has a large working deck and hull for installing auxiliary systems such as compression and H2 bunkering.
The company’s focus on using a novel design concept to build a completely new value chain has seen other energy interests investigate the potential of compression technology in shipping.
The co-operation between ABS and Provaris also demonstrates that progress can be achieved in the energy transition even when considering completely new approaches. The completion of the class-approval process will enable Provaris to move forward with an initial vessel order that can take its place in the new value chain.